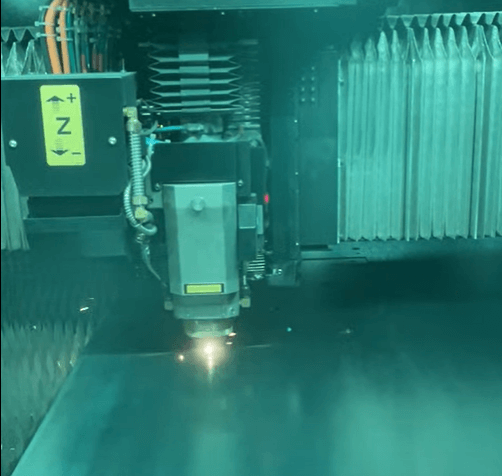
高精度切断技術でステンレスレーザー加工を革新する方法
目次
1|ステンレスレーザー加工の基本原理
レーザー加工は、集中的なレーザービームを使用して金属材料を切断する先進的な方法です。ステンレスの加工において、レーザー技術は高い精度と効率を実現します。この技術では、レーザービームがステンレスの表面に照射され、その熱エネルギーによって材料を溶かし、蒸発させることで切断を行います。
加工時には、アシストガスと呼ばれる補助ガスを使用し、溶けた金属を吹き飛ばすとともに、切断面の酸化を防ぎます。一般的に、窒素ガスや酸素ガスが使用され、材料の特性や求められる品質に応じて最適なガスが選ばれます。
2|高精度切断を実現するための重要要素
①レーザー出力の最適化
高精度な切断を実現するためには、材料の厚さや種類に応じて適切なレーザー出力を設定する必要があります。出力が強すぎると切断面が荒れ、弱すぎると切断が不完全になる可能性があります。
②切断速度の制御
切断速度は加工品質に大きく影響します。速度が速すぎると切断不良が発生し、遅すぎると熱影響部が大きくなります。材料の厚みや求められる精度に応じて、最適な切断速度を設定することが重要です。
③焦点位置の調整
レーザービームの焦点位置は、切断品質に大きく影響します。材料表面での適切な焦点位置を維持することで、均一な切断品質を確保できます。
3|最新の技術革新と改善点
①自動焦点制御システム
最新のレーザー加工機では、自動焦点制御システムを搭載し、常に最適な焦点位置を維持することが可能です。これにより、安定した切断品質を実現できます。
②インテリジェント制御システム
AIを活用した制御システムにより、材料の状態や切断条件をリアルタイムで監視し、最適なパラメータを自動調整することが可能です。
③高効率冷却システム
新世代の冷却システムにより、長時間の連続運転でも安定した加工品質を維持できます。これにより、生産性の向上と品質の安定化が実現されています。
4|品質管理と精度向上のポイント
①切断面品質の評価
- 表面粗さの測定
- 垂直度の確認
- バリの有無のチェック
- 熱影響部の評価
②加工条件の最適化
- 材料厚みごとの最適条件設定
- アシストガス圧力の調整
- ノズル位置の最適化
- 切断パターンの最適化
③設備メンテナンス
定期的なメンテナンスにより、装置の性能を最大限に発揮させることが重要です。特に以下の点に注意が必要です:
- レーザー光学系の清掃
- ノズルの点検と交換
- 各種センサーの校正
- 冷却システムの点検
5|加工における注意点と対策
①熱変形の防止
- 適切な切断順序の設定
- 熱影響を考慮した加工パターンの選択
- 必要に応じた冷却時間の確保
②材料特性への配慮
- ステンレスの種類による加工条件の調整
- 表面状態の確認
- 材料厚みのばらつきへの対応
③環境要因の管理
- 作業環境の温度・湿度管理
- 防塵対策
- 適切な換気システムの確保
これらの技術と管理方法を適切に組み合わせることで、高精度なステンレスレーザー加工が実現可能になります。常に最新の技術動向を把握し、継続的な改善を行うことで、さらなる品質向上と効率化を図ることができます。
当社は、最新のレーザー加工技術を用いて、お客様のニーズに応じた高精度な加工サービスを提供しています。ステンレスレーザー加工についてのご相談は、お気軽にお問い合わせください。