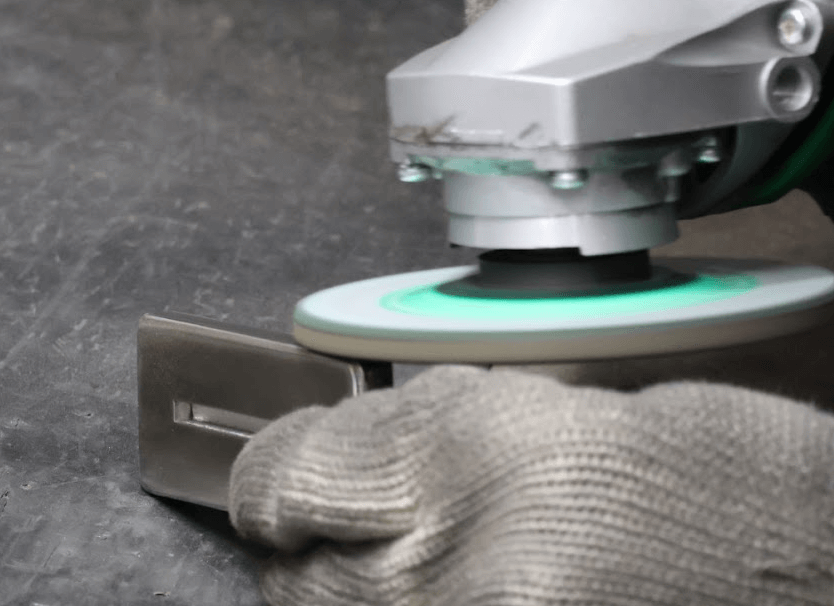
表面品質改善とスキンパス圧延の重要性:製造業の最新トレンド
はじめに
製造業において、製品の品質は企業の競争力を左右する重要な要素です。この品質の中でも、表面の滑らかさや光沢、傷や打痕の有無など、視覚的・機能的な面での仕上がりは非常に大きな影響力を持ちます。実際に、金属板や鋼板などの素材における表面の美観や性能は、最終製品の付加価値を左右し、顧客満足度にも直接関わるため、企業にとって非常に重要な課題となっています。
表面品質が優れているかどうかは、製品の寿命や耐久性にも影響を与えます。たとえば、自動車や家電製品、産業用の機械部品など、広範な分野で表面が美しく、傷つきにくい素材は高く評価されます。そこで注目されるのが、スキンパス圧延と呼ばれる加工技術です。冷間圧延後の鋼板を軽く圧下することで表面の平坦度を高め、微細な傷や凹凸の発生を抑えるこの工程は、各種金属製品の仕上がりを飛躍的に向上させる可能性を秘めています。
本記事では、スキンパス圧延とは何か、その歴史と進化、そして表面品質改善に及ぼす役割について、さまざまな角度から解説していきます。さらに、最新の技術トレンドや実践的な事例、そして環境への配慮と持続可能性にも触れながら、製造業の未来におけるスキンパス圧延の重要性を考察します。
まずは「表面品質」とは何を指し、その改善がなぜこれほどまでに重視されるのかを見ていきましょう。表面品質がもたらす効果や、製造業全般における役割を理解することが、スキンパス圧延の本質に近づく第一歩となります。
表面品質は、材料の保護膜としての役割や、接触面の抵抗低減機能、あるいは製品のブランドイメージを左右するデザイン上の要素など、多面的な意味を持ちます。そのため、つや消し表面が好まれる用途や、高い光沢が求められる高級製品など、各用途に応じて適切な表面仕上げが必要とされるのです。また、表面に発生する微細な傷や凹凸は、応力集中を招く場合があり、材料の強度低下や疲労破壊に繋がることがあります。これは自動車、航空機、産業機械など、安全性が最優先される分野において、とりわけ重要な問題です。
一方で、外観品質は顧客が製品を選定する際の大きな評価基準ともなります。高級感を演出するステンレス製品や家電、パッケージ素材など、ユーザーの最初の接点である「見た目」が、企業の信頼性や製品価値を左右することは少なくありません。こうした背景から、スキンパス圧延を含む表面仕上げ技術は、単なる最終工程ではなく、製品開発の初期段階から考慮されるようになりました。素材の選定、圧延条件の設定、焼鈍や研磨などの後工程との連携が、最終的な品質を左右するためです。
次の章では、スキンパス圧延そのものの基本概念と、その技術がどのように発展してきたのかを解説し、製造業にとっていかに不可欠な存在となっているのかを紐解いていきます。
スキンパス圧延とは
スキンパス圧延は、調質圧延やテンパーローリングとも呼ばれる工程で、主に冷間圧延後に焼鈍を施した鋼板などに対して行われる、数%以下の軽い圧下による圧延方法を指します。その目的は、最終的な鋼板の表面特性を高めることや、板厚や平坦度のばらつきを最小限に抑えることなど、多岐にわたります。
この工程で得られる最大の利点の一つが、表面粗さの制御です。圧下率を微調整することで、最適な光沢や表面硬度を実現できるため、自動車パネルから家電の外装パネル、建築素材に至るまで、幅広い分野で幅広い要求特性に対応することが可能です。
スキンパス圧延の歴史を振り返ると、薄板材の需要が拡大し始めた時代に、その表面品質や寸法精度を安定的に確保する手段として注目を集めました。圧延技術が進歩する中で、単に材料を薄く延ばすだけでなく、表面の仕上がりや強度特性を微調整できる工程として発展してきたのです。当初はスキンパス圧延による付加価値は限定的と捉えられましたが、市場からの厳格な品質要求や、多様化する製品ラインナップへの対応が求められるにつれ、製造プロセスにおいて欠かせない最終仕上げ工程となりました。
歴史が進むにつれ、スキンパス圧延にも新たな技術が導入されてきました。例えば、ロールの表面に特殊なパターンを作り出し、エンボス効果を付与する技術が開発されるなど、単なる圧下だけでなく、意匠性や機能性を向上させる工夫が進んでいます。こうした進化を経て、現代のスキンパス圧延は、多くの製品で「最後のひと手間」として表面品質の確保を支えるだけでなく、製品に新たな付加価値を与える手段としても利用されるようになりました。
次章では、なぜこの技術が表面品質改善の要として重視されるのか、その背景を具体的な製品性能や顧客満足度との関係から探っていきます。
表面品質改善の重要性
一般的に、金属製品の表面状態は、美観だけでなく、耐食性や摩擦特性、さらに疲労強度などにも影響します。微細な傷や凹凸があると、そこに汚れや水分がたまりやすくなるだけでなく、応力集中の原因ともなり得るため、表面を滑らかに仕上げることはきわめて大切です。また、高い光沢や独特の模様が施された表面は、製品に高級感や差別化を与え、ブランド力の向上にも寄与します。例えば、家電や自動車の外装など、外観に大きな影響を及ぼす製品では、製品デザインの一部として表面処理が意識的に取り入れられています。
顧客満足度を左右する要素としても、表面品質は無視できません。鉄やステンレスなどの素材は、傷が目立ちやすい性質を持つ場合が多く、消費者からのクレームや返品リスクを低減するためには、高い表面品質を確保することが必要不可欠になります。さらに、表面品質が実際の使用環境での性能に深く影響を及ぼす例としては、耐食性の向上が挙げられます。スキンパス圧延によって均一な表面が得られることで、塗装やメッキなどの後工程の品質も安定し、最終的な耐久年数に大きく寄与するのです。
市場で競合他社との差別化を図るうえでも、表面品質は重要な戦略的要素となります。見た目の印象が購入者の意欲を左右する製品では、いかに魅力的で信頼感のある仕上がりを実現できるかが大きな課題。この課題を解決するためのキーとなる技術の一つが、スキンパス圧延なのです。以上のように、表面品質の改善は単なる外観上のこだわりではなく、製品の性能、耐久性、そして顧客の満足度に深く関連する重要なテーマです。
次の章では、スキンパス圧延が実際にどのような影響を製品にもたらすのか、その具体的なメカニズムについて掘り下げてみましょう。
スキンパス圧延が表面品質に与える影響
スキンパス圧延が表面品質を向上させる大きな要因の一つは、圧下率を数%以下に抑えた「軽圧下」によって生じる微細な加工硬化効果です。これにより、素材の表面は均一に引き伸ばされ、毛羽立ちや小さな凹凸が効果的に抑えられます。結果として、鏡面に近い光沢を得ることも可能となります。また、スキンパス圧延においては、素材を引き伸ばしながら圧延することで、薄板の板厚精度や平坦度が向上し、後工程でのトラブルを大幅に低減できます。この加工によって得られた製品は、共同作業として行われる塗装やメッキ、さらにはプレス成形などで、より安定した品質を提供します。
表面粗さの低減は、特に腐食性や衛生面が重視される環境下での使用に大きく貢献します。食品産業用のステンレス容器や医療器具など、菌や汚れの付着を防止したい製品では、スキンパス圧延による平滑な表面が求められます。さらに、機械的性質の改善という点では、スキンパス圧延によって導入される微細なひずみが、素材に程よい硬さを与える場合があります。完全な焼鈍状態よりも適度に硬度が高まることで、傷やへこみへの耐性が増し、長期的な耐久性が向上することが知られています。
ただし、加工硬化が過剰になると、逆に割れやすさが増すリスクもあるため、圧下率や工程条件の設定には高度なノウハウが必要です。素材の種類や最終用途、要求される物性を総合的に考慮しながら最適値を導き出すことが、現場のエンジニアにとっての大きな挑戦となります。このように、スキンパス圧延は表面の光沢や滑らかさの向上だけにとどまらず、材料全体の機械的特性にも好影響を与えるため、まさに製品品質を左右する重要な工程と位置づけられています。
では、次に、近年の技術革新や新しい素材の登場によって、スキンパス圧延の世界がどのように変化しているのかを見ていきましょう。
最新トレンド:技術革新とスキンパス圧延
近年、製造業では新素材の研究開発が盛んに行われており、高強度鋼板や耐熱合金など、従来よりも高い性能を持つ材料が次々と登場しています。これらの新素材を活用するうえで、スキンパス圧延の技術もまた進化を遂げる必要があります。圧延ロールの材質、表面処理、さらには圧下制御のアルゴリズムなど、さまざまな分野で革新的な取り組みが行われています。
とりわけ、自動車業界では軽量化と高強度化が求められており、超ハイテン材と呼ばれる高張力鋼板が注目を集めています。これらの薄くて強い鋼板を扱う際に、スキンパス圧延によって表面品質や寸法精度を保つことが、製造工程の安定化と性能確保の要として機能しているのです。
さらに、デジタル技術の導入はスキンパス圧延にも大きな変革をもたらしています。センサーやAIを活用したプロセスモニタリング、デジタルツイン技術による工程シミュレーションなど、リアルタイムで圧延条件を最適化する取り組みが加速。これによって、均一な品質を大量生産の現場で確保しながら、ロスを最小限に抑えることが可能となりました。自動化も進みつつあり、かつては熟練工の経験や勘に頼っていた微妙な圧下率やロール交換のタイミングなどが、データ解析によってより客観的、効率的に管理できるようになっています。結果として、品質のばらつきが減少し、安定した生産性を維持することが可能となりました。
一方、新素材への対応だけでなく、エンボス加工やヘアライン仕上げなど、装飾性・機能性を付加するための圧延技術も発展しています。特に建材やインテリア、家電のパネルなどでは、高い意匠性と実用性を兼ね備えた表面仕上げが求められるため、多彩なロール表面加工技術が開発されています。こうした技術革新により、スキンパス圧延は単なる品質安定の手段から、製品の付加価値を高めるためのキー技術へと変貌を遂げています。
次の章では、実際にどのような現場でこの技術が活用され、どのような成果を生み出しているのかを実践例とともに見ていきましょう。
スキンパス圧延の実践例
スキンパス圧延は、幅広い分野で採用されていますが、その中でも自動車業界と家電業界の事例は特に注目に値します。自動車用の外装パネルでは、表面の平坦度や傷の少なさが外観品質を大きく左右しますが、スキンパス圧延を導入したメーカーでは、塗装後の仕上がりが飛躍的に向上し、クレーム数が大幅に低減したという報告があります。
家電業界では、スタイリッシュな外装を実現するためにステンレスやアルミニウムなどが多用されます。これらの金属素材にスキンパス圧延を施すことで、指紋や細かな傷を目立ちにくくする表面仕上げを実現し、ユーザーの満足度向上につなげているケースが増えています。一方、建設資材の分野でも、大型パネルや屋根材などにスキンパス圧延した鋼板が用いられることで、美観と耐久性を両立させる取り組みが進んでいます。特に商業施設や公共建築物など、意匠性が求められる場面で高品質な外装材として評価を得ています。
さらに、食品加工や医療機器など衛生面が重視される領域では、スキンパス圧延による平滑性が洗浄の容易さや菌の繁殖抑制につながるため、クリーンな環境を維持するうえで大きなメリットを発揮しています。製造から消費、廃棄に至るまでのライフサイクル全体で評価される品質が求められる時代にこそ、この技術の価値が顕在化するのです。
たとえば、あるメーカーでは、スキンパス圧延機に最新のAI制御システムを導入し、ロールの劣化や圧下率の微細な変化をリアルタイムに補正することで、常に一定品質の製品を生み出すことに成功しています。この事例では、不良率の低減や生産スピードの向上だけでなく、予防保全を含めたトータルコストの削減にも貢献できたとされています。
このように、理論だけでなく、多数の成功事例がスキンパス圧延の有用性を裏付けています。次章では、近年ますます注目される環境への配慮や、持続可能な製造プロセスづくりにおいて、スキンパス圧延がどのような役割を担っているのかを探ります。
環境への配慮と持続可能性
製造業における環境配慮の重要性は年々高まっており、二酸化炭素排出量の削減やエネルギー効率の向上、廃棄物の削減などが強く求められています。スキンパス圧延にも、これらの流れに対応するための取り組みが進められています。
まず、エネルギー効率の向上という観点からは、軽圧下とはいえスキンパス圧延に必要な動力をいかに最適化するかが課題となります。近年では、インバータ制御や高効率モーターの採用、摩擦損失を低減させる潤滑技術の開発などによって、圧延工程全体のエネルギー使用量を抑える試みが行われています。
また、スキンパス圧延によって表面品質を向上させることは、後工程の塗装やメッキの歩留まりを高め、不良品の再加工や廃棄を減らす効果も期待できます。素材を無駄にしないという意味で、資源循環の観点からも意義の大きい技術でしょう。さらに、廃棄物削減への取り組みにおいては、ロール交換のサイクルを伸ばす技術開発や、メンテナンス性の向上による部品リユースなどが注目されています。ロールはスキンパス圧延で常に高い負荷を受けるため、表面の損傷を最小限に抑える表面処理技術の進化が欠かせません。
持続可能性の視点からは、人件費の削減だけでなく、労働環境の改善も重視されます。自動化やAIの活用により、作業者が危険な環境に長時間さらされることが減り、安全性と効率性を両立する製造ラインの構築が可能となります。これは、企業の社会的責任(CSR)やESG投資などの観点からも、非常に高い評価を得るポイントです。
このように、スキンパス圧延は品質向上だけでなく、環境負荷軽減や持続可能な産業基盤の構築にも寄与する重要な技術です。最終章では、今後のスキンパス圧延がどのように進化し、製造業の未来を支えていくのか、その展望をまとめていきます。
まとめ
スキンパス圧延は、製品の最終品質を大きく左右する重要な工程です。数%以下という軽圧下ながら、表面の光沢や平坦度を最適化し、機械的特性をコントロールすることができます。結果として得られる高い表面品質は、製品の耐久性や美観、そして顧客満足度を向上させる大きな要素となっています。
技術革新の観点からは、新素材への対応やAI・自動化の導入、さらには多様な表面模様の付与など、近年のスキンパス圧延はその可能性を大きく広げています。単なる品質安定手段から、高付加価値を創出するためのキー技術へと進化を遂げており、製造業にとって欠かすことのできない存在であるといえるでしょう。また、環境への配慮や持続可能性の側面でも、スキンパス圧延が果たす役割は大きいです。高精度な表面仕上げが歩留まりの向上に寄与し、廃棄物を削減するだけでなく、エネルギー効率の向上や自動化による安全性改善にも直接つながっています。
これからの製造業は、一層の品質向上とコスト削減、そして環境への責任が求められる時代を迎えます。その中で、スキンパス圧延の存在意義は増すばかりです。新しい素材やニーズに柔軟に対応しつつ、最新技術を積極的に取り込みながら、製造プロセスの革新を支えていくでしょう。今後、さらなる高速化や精密化が進んだスキンパス圧延機が登場し、デジタル技術との連携が進むことで、より安定した品質や多様な表面仕上げを実現できる未来が予想されます。これにより、製造業全体の国際競争力が高まると同時に、社会的課題の解決にも寄与するはずです。
最後に、スエナミ工業では、スキンパス圧延に関連するさまざまな技術と製品を取り揃えています。高品質なステンレス加工や精密なロール研磨技術など、多角的なノウハウを活かし、お客様の多様なニーズに応えられる体制を整えているのが強みです。スキンパス圧延をはじめとする先端の圧延ソリューションを通じて、表面品質改善と製造コストの最適化を実現したい企業の皆様に、ぜひご検討いただきたい製品群です。以上のように、スキンパス圧延は材料の微細な調整を可能にする技術であり、製造業における品質向上と差別化の重要な鍵を握っています。これを上手く活用することで、激化する市場競争の中で企業が生き残り、発展していくための武器となるでしょう。