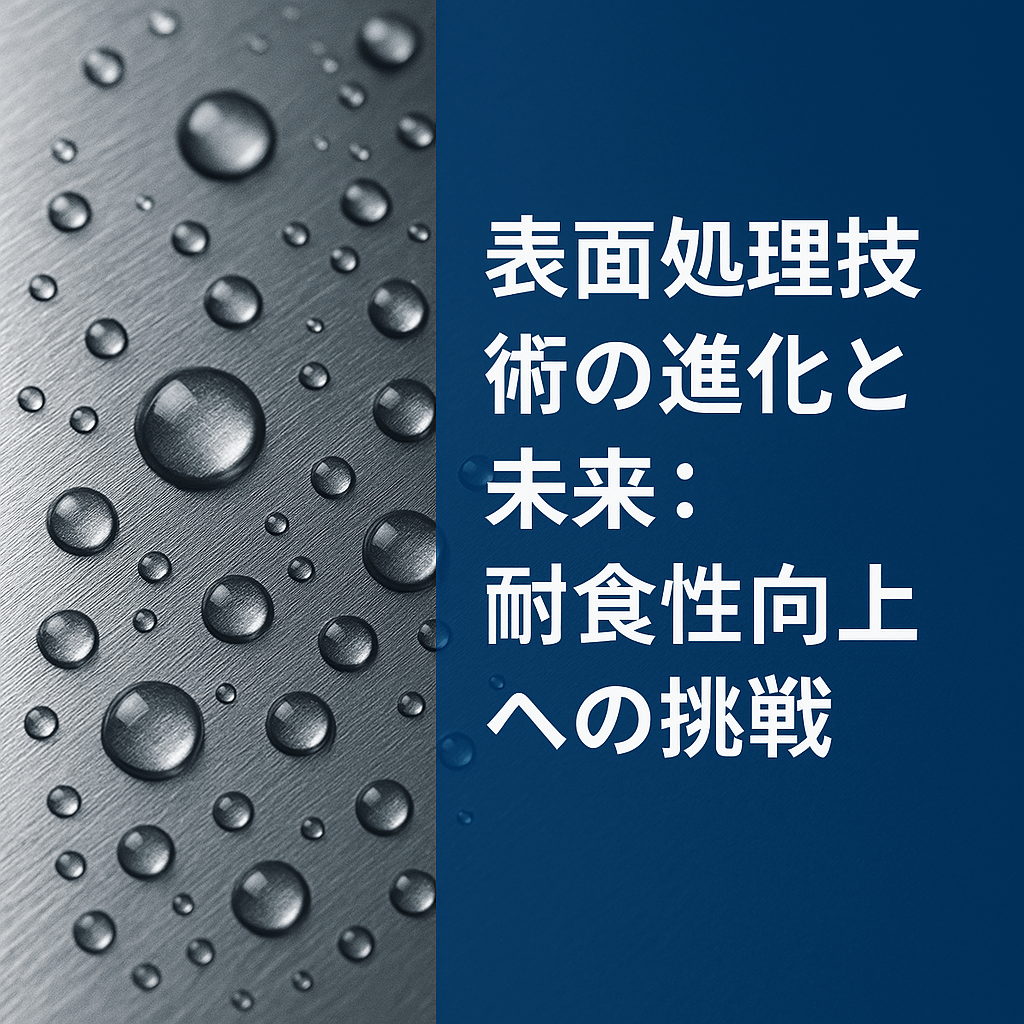
表面処理技術の進化と未来:耐食性向上への挑戦
序章
表面処理技術は、材料の表面に特定の機能や特性を付与するための重要な工程です。例えば、金属表面を耐摩耗性や耐食性に優れた状態へと改質することで、部品の長寿命化を図ります。このように、多様な産業で基盤となる技術です。加えて、表面処理は製品の外観品質を向上させる上でも重要であり、高付加価値化を実現するために欠かせない工程となっています。新素材・技術の進歩によりその可能性は高まっています。
近年では、持続可能性への関心が高まり、環境に配慮した表面処理法への需要が一段と増しています。たとえば有害物質の使用を抑制する技術開発や、省エネルギー化に向けた研究が進められています。この潮流は企業の社会的責任を果たす上でも大きな意味を持ち、表面処理における資源の有効活用や排出物の低減策は、今後ますます重要視されるでしょう。表面処理分野の研究者は新素材と新工程を絶えず追求しています。
本記事では、表面処理技術の歴史と進化、基本メカニズム、そして耐食性を高める最新技術などを順に概説します。さらに産業別の応用事例や直面している課題を捉え、その先にある未来像を探ります。表面処理技術は多種多様な手法がありますが、基本を理解することで応用範囲が一層明確になります。ぜひ最後までご覧いただき、表面処理がもたらす可能性を実感してください。章立てを通じ、知見を得られるよう願います。
歴史と進化
表面処理技術は古代から存在しており、当初は金属の美観向上や装飾が主目的でした。古代エジプトやギリシャでは貴金属を用いたメッキに類する技法が見られ、その繊細さで人々を驚かせました。こうした装飾中心の技術は、のちに武具や道具へも応用され、耐久性や防錆効果を狙った処理へと発展していきます。伝統技術として今日まで受け継がれた例も少なくありません。古今東西から表面処理の多様性はうかがえます。
中世から近世にかけては、武器の強化や船舶の防食策として表面処理がさらなる発展を遂げました。鉄を錆びにくくする技法や、青銅像の美観保持など、多岐にわたる工夫が見られます。大航海時代には船底に防食コーティングが施され、海水からの腐食を防ぐ手段として確立。各地の気候や海洋条件に合わせて改良が重ねられ、人類の活動範囲拡大を支えました。環境に合わせた改良が、近代表面処理技術の礎となりました。
産業革命以降、蒸気機関や鉄道の普及に伴い、大量生産が加速するとともに表面処理の役割も拡大しました。塗装やめっき技術は工業製品の長寿命化と差別化に大きく寄与します。大量生産に適した高速処理方法も開発され、特に自動車や家電製品などでは、美観を保ちながら性能や耐久性を向上させる目的で各種コーティング技術が取り入れられました。製造現場では表面処理が欠かせない工程と認識されるようになりました。
基本メカニズム
表面処理を大きく分類すると、主に「電気めっき」「化学めっき」「物理蒸着(PVD)」「化学蒸着(CVD)」「熱処理」といった手法が挙げられます。電気めっきでは外部電源を利用して金属皮膜を生成し、化学めっきでは触媒作用を利用して基材の表面に金属皮膜を析出させます。いずれも均一で安定したコーティングを得ることが目的です。
物理蒸着(PVD)では、真空中で金属やセラミックなどの材料を蒸発させ、イオンや分子の形で基材表面に堆積させます。化学蒸着(CVD)では、ガス状の化学物質を用いて化学反応を起こし、薄膜を形成します。これらの蒸着技術は半導体や光学部品などの高度な分野でも不可欠な存在です。
熱処理は金属の組織を制御し、硬度や耐久性を向上させる手段ですが、表面硬化処理として用いる場合には、炭素や窒素を浸透させる熱化学処理が一般的です。表面にのみ高い硬度を与え、内部は比較的柔軟性を保つため、衝撃などに強い特性を得られます。
耐食性向上のための最新技術
素材が酸化や腐食によって劣化するのを防ぐことは、多くの産業にとって死活問題です。近年では、ナノテクノロジーを駆使した薄膜コーティングが注目されています。原子レベルで均一な膜を形成することで、従来よりも高い防食効果を発揮し、さらに軽量化や機能統合にも寄与します。
複合コーティングも盛んに研究されており、セラミックスや金属粒子を混合した複合材料による多機能膜が開発されています。たとえば、研磨粒子を含むコーティングで高い耐摩耗性と耐食性を両立させるなど、従来は相反する特性を同時に実現する手法が増えつつあります。
また、新素材の探索も耐食性向上の重要なアプローチです。従来のステンレス鋼を超える耐腐食性を持つ合金や、高分子材料とのハイブリッドコーティングなど、研究が活発化しています。これらの材料技術と表面処理技術の組み合わせにより、大幅な寿命延長やメンテナンス軽減が期待されています。
産業別に見る表面処理技術の応用
自動車産業では、車体やエンジン部品に対して耐久性や外観品質を確保するために塗装やめっきが活用されます。特に排気系部品など過酷な環境にさらされる箇所には、高性能コーティングが施され、錆や腐食を防止することで安全性と信頼性を維持します。
航空宇宙産業では、部品の軽量化と高信頼性が求められます。高温や強い圧力変化に耐えるため、耐熱性や耐摩耗性に優れた表面処理が実装されます。先端的なPVDやCVD技術は航空機エンジンの部品や宇宙機器の保護膜として不可欠な存在です。
電子機器産業では、半導体やプリント基板など極めて繊細な部品の表面保護が不可欠です。微小な汚染や酸化でも性能に影響が出るため、クリーンルーム環境での薄膜コーティングが用いられます。防湿や放熱を目的としたコーティングもあり、スマートフォンなどの耐久性にも大きく寄与しています。
表面処理技術の課題と解決策
一方で、表面処理技術にはいくつかの課題も存在します。代表的なものとして、環境への負荷が挙げられます。めっき工程で使用する化学物質や廃液の処理、排ガスによる大気汚染など、適切な処理を行わなければ生態系への影響は深刻です。近年はグリーンケミストリーの視点を取り入れ、有害物質を極力使用しないプロセスの開発や、廃水の再利用技術が進展しています。
また、コスト効率の問題も深刻化しています。高性能なコーティングほど工程が複雑化し、エネルギー消費量も増大しがちです。そのため、生産性を保ちながら品質を向上させるための自動化技術や省電力化装置の導入が進められています。IoTやロボット技術と組み合わせ、最適なプロセス管理を行う取り組みも増加しています。
技術的限界の克服も課題の一つです。特に極端な環境、例えば高温・高圧下や宇宙空間などでは、従来の表面処理だけでは十分な性能を発揮できないケースがあります。新素材の導入や複合処理、さらにはレーザーやプラズマを活用した先端プロセスが、これらの限界を打破する鍵として期待されています。
未来の表面処理技術
今後はAIやIoTとの連携が、表面処理技術に新たな次元をもたらすと予想されます。機器の稼働状態や周囲環境のデータをリアルタイムで分析し、最適なコーティング条件を自動で調整するシステムが構築されるでしょう。これにより、生産効率の向上と品質の安定化が同時に実現される可能性があります。
持続可能な技術開発の方向性としては、再生可能エネルギーを利用した加熱プロセスや、廃棄物ゼロを掲げるクローズドシステムの確立が期待されます。さらに、バイオマテリアルを活用した環境調和型コーティングなど、新たな視点からのアプローチも増えてきています。
グローバル市場では国際競争が激化する中、各国の規制や産業構造の違いに合わせて技術を最適化する動きが加速するでしょう。一方で、研究開発の国際協力が進むことで、革新的な素材や処理方法が世界的に共有されるようになり、表面処理技術の進化スピードはさらに加速すると考えられます。
まとめ
表面処理技術は古代の装飾から始まり、多種多様な産業の発展を支えてきました。現代では、防食や美観、機能性向上など多面的なニーズを満たす総合技術へと成長しています。とりわけ耐食性向上に関しては、ナノテクノロジーや複合材料の登場によって一段とブレイクスルーが期待される段階にあります。
これからもさらなる技術革新が進めば、重要部品のメンテナンス周期が延び、コスト削減や環境負荷の低減が同時に実現されるでしょう。産業界のみならず、人々の生活や安全に深く関わる技術として、継続的な挑戦が求められています。
今後、表面処理技術の役割はより重要性を増し、その可能性は一層大きく広がるはずです。企業や研究機関が連携し、新たな素材や処理プロセスを発掘・開発することで、地球環境との共生を図りながら持続的な成長を続けられる未来が見えてきます。
スエナミ工業の製品推薦
今回のコラムで述べたように、耐食性や耐摩耗性を高める表面処理技術は、多様な産業分野で不可欠な存在となっています。スエナミ工業では、最新の表面処理技術と長年培ったノウハウを融合させ、厳しい環境下でも性能を発揮する高品質な製品を提供しています。
特に、特殊合金メッキやナノ粒子を活用したコーティングなど、先端的な技術を柔軟に活用できるラインナップを取り揃えています。製品寿命の向上やメンテナンスコストの削減をお考えの方は、ぜひスエナミ工業の各種表面処理サービスをご検討ください。