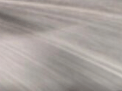
多軸水平研磨技術: 製造業における革新的な表面仕上げの未来
はじめに
製造業において、部品や製品の品質を左右する重要な要素の一つが表面仕上げです。多様な素材や複雑な形状を扱う現代の生産現場では、美観や機能性、耐久性など、あらゆる観点から高精度な表面加工が求められています。また、近年では小ロット多品種生産や短納期化にも対応すべく、研磨技術にもより柔軟なアプローチと効率化が求められています。
こうした背景の中で注目を集めているのが、多軸水平研磨技術です。従来の研磨方式では、一般的に研削砥石やベルトなどを使用し、一方向または限られた方向に研磨することが多くありました。しかし、多軸水平研磨技術を導入することで、従来の技術では困難だった複雑形状への対応や、素材の特性を活かした繊細かつ均一な仕上げが実現可能となります。
本記事では、多軸水平研磨技術が持つ優れた特徴や具体的な活用事例を通して、その技術的基盤とメリット、さらには生産コストや環境負荷削減への影響など、多方面から詳しく解説します。本コラムを通じて、次世代の研磨プロセスがもたらす可能性を探究し、製造業界がどのように変化していくのか考察していきます。
特に、精密加工や装飾性が強く求められる分野では、多軸水平研磨技術による均一かつ美しい表面処理が高く評価されています。生産ラインの自動化や人手不足への対応にも大きく貢献できるため、この技術は今後さらなる注目と発展を遂げることでしょう。
多軸水平研磨技術の概要
多軸水平研磨技術とは、回転する複数の研磨ツールやブラシ、あるいは砥石を同時または段階的に制御することで、対象物の表面に対して多方向から均一な研磨を行う技術を指します。一般的には、高精度な制御装置やセンサー技術と連動し、加工条件を最適化することで、従来よりも短時間で高品質な仕上げを実現します。
従来の研磨工程では、一方向に強い研磨痕が残りやすいため、最終製品の外観品質や特定部位の摩耗・劣化に悪影響を及ぼすことがありました。しかし、多軸水平研磨技術を用いることで、多方向から微細な研磨を施すことができ、製品表面の凹凸を均一化しながら光沢や触感を向上させることが可能となります。
また、この技術では、加工プログラムを細かく設定することで、素材や形状の特性に合わせた最適な研磨パターンを構築できます。例えば、薄肉の金属板を扱う場合には、圧力や速度を微調整して変形を最小限に抑えつつ高い仕上げ精度を保つことが可能です。一方、硬度が高い合金素材に対しても、複数の軸を活用することで均等に力を分散し、局所的な熱変形やクラックの発生を防げる点が大きな強みとなります。
さらに、多軸水平研磨技術はオペレーターの熟練度に左右されにくいというメリットも存在します。従来の手作業や単軸研磨では、職人の技巧や経験が品質に直結していましたが、多軸制御技術を導入することで、一定の品質基準を安定して満たすことができ、作業者の負荷軽減や生産性向上につながります。
革新性と利点
多軸水平研磨技術の最大の革新性は、研磨痕を局所化させずに均一な仕上げを行える点にあります。これにより、従来のベルト研磨やディスク研磨では困難だった高度な意匠性や機能性が求められる部品でも、美観と精密性を同時に実現することが可能です。特に曲面や凹凸がある部品で高い効果を発揮し、表面の粗さを微細にコントロールできます。
また、多軸水平研磨技術は効率性の面でも大きなメリットをもたらします。複数の軸を同時に稼働させることで、研磨工程を一括して行うことができるため、従来の単軸方式と比べて加工時間を大幅に短縮できます。結果として、トータルコストの削減と量産体制の強化につながり、多品種少量生産から量産まで幅広い生産形態に柔軟に対応可能です。
加えて、環境面への配慮もこの技術の利点の一つです。最適化された研磨条件を設定することで、研磨剤の使用量を削減できるほか、廃棄物の発生や作業現場における振動や騒音などの負荷も低減できます。エネルギー効率の面でも、研磨時間の短縮や均一な研磨プロセスにより、余計な電力消費を抑えられる可能性が高まります。
さらに、多軸水平研磨技術は高精度な制御システムを前提としているため、加工パラメーターのデジタル管理が容易となります。このデジタライゼーションにより、研磨プロセスの履歴や品質データを蓄積しやすくなり、工程改善やトレーサビリティの確保にも大きく貢献します。これにより、品質保証活動や不良率低減がより精密かつ迅速に進められるようになります。
多軸水平研磨技術の応用分野
まず、自動車産業では、多軸水平研磨技術がエンジンやシャーシ部品、さらに内外装パーツの表面加工に広く活用されています。高温・高負荷に耐えねばならないエンジン部品に対しても、均一な研磨仕上げを施すことで、摩耗を抑え寿命の延長を図ることが可能です。また、カーデザインの美観を維持する観点からも、外装パネルや装飾パーツへの微細な研磨が求められています。
航空宇宙産業では、軽量化と強度を両立させるための素材として、アルミ合金やチタン合金が数多く使用されます。多軸水平研磨技術を取り入れることで、複雑な形状の翼やエンジンコンポーネントに対しても研削痕を極力残さず、高精度な仕上げを実現できるのです。これにより、飛行中の空気抵抗や応力集中を低減させ、乗り物全体の性能や安全性を向上させることが期待されています。
医療機器製造の分野でも、この技術は不可欠な存在となりつつあります。ステンレスやチタンなどの生体適合性金属を使用した医療機器では、患者の体内に接触する部分の表面仕上げが極めて重要です。多軸水平研磨を用いることで、装置の角や表面の微細なバリを除去し、安全性と衛生面での信頼性を高めることができます。さらに、デリケートな形状を保持しながら高精度な加工を実現できる点でも大きな利点があります。
電子部品製造では、小型化や高機能化が進む中で、部品の寸法精度だけでなく表面品質も厳しく要求されます。多軸水平研磨技術を利用すれば、極小部品のエッジや微細な溝部分など、従来であれば手間や時間がかかっていた場所でもスムーズに研磨が行えるため、生産の効率化と品質向上を同時に実現し、競争力アップにつなげることができます。
成功事例
多軸水平研磨技術を導入した企業の成功事例としては、自動車部品の製造ラインにこの技術を組み込んだケースが挙げられます。例えば、アルミホイールやエンジンのシリンダーヘッドなど、これまで研磨時間や品質安定性に課題があった部品を対象に多軸水平研磨システムを導入したところ、加工速度が大幅に向上し、不良率の低減にも大きく寄与しました。
ある企業のインタビューによれば、従来は複数の工程と手作業を繰り返し行わなければならなかった研磨作業が、多軸水平研磨技術の実装によって一元化し、作業者の負担と人件費を削減できたと言います。さらに、不完全な研磨痕やバリが原因となるトラブルが激減し、品質保証コストも削減されました。
また、航空宇宙分野においては、チタン合金製のエンジンブレードの品質向上と耐久性確保に大きく貢献した事例があります。従来の研磨方式では、ブレード表面にわずかな傷が残ることで応力集中が生じやすく、耐久性が懸念されるケースもありました。しかし、多軸水平研磨によって高精度の表面状態を得られるようになり、飛行試験の結果、金属疲労の発生率が著しく低下したことが報告されています。
医療機器メーカーの導入事例では、人工関節や歯科インプラントなどの加工工程において、多軸水平研磨技術が部品の寿命と安全性を高める要因として評価されています。極めて滑らかな表面を得ることで、患者の体内への刺激を最小限に抑え、感染リスクの低減にも寄与します。このように、さまざまな業種で導入が進み、高い評価を得ている点が多軸水平研磨技術の大きな特長です。
導入における課題と解決策
多軸水平研磨技術のメリットは多いものの、導入時にはいくつかの課題も存在します。まず、設備導入コストが比較的高額になることが挙げられます。高精度なセンサーや複数の軸を同時に制御するシステムを設置するため、初期投資がかさむ場合があります。ただし、長期的には生産性向上や不良率低減といった効果によって、投資回収が見込めるケースが多いとされています。
次に、人材育成の問題があります。多軸制御や研磨用プログラムの最適化を行うには専門知識が必要であり、新たに導入した企業では作業者に対するトレーニングやシステム管理者の育成が求められます。これに対しては、装置メーカーやシステムインテグレーターが提供する研修プログラムやサポートサービスを積極的に活用することが有効です。
また、従来の生産ラインとの統合や、既存工程との相性を検討する必要があります。多軸水平研磨機を導入したことで他の工程のボトルネックが生じる可能性もあるため、ライン全体の最適化を見据えた設備配置や生産計画が重要です。この課題に対しては、事前に十分なシミュレーションや試験導入を行い、段階的に稼働範囲を広げるといった手法が一般的に用いられています。
最後に、メンテナンスや部品交換時の管理も欠かせません。多軸水平研磨技術は高度なメカトロニクス技術が組み合わさっているため、不具合が発生した際には迅速な修理対応や専門知識が必要です。予防保全として定期的な点検を行うほか、装置の状態を常時モニタリングするシステムを導入することで、故障リスクを最小限に抑えることができます。
今後の展望と未来の可能性
多軸水平研磨技術は今後ますます進化し、製造業界の多様なニーズに対応する可能性を秘めています。今後はAIやIoT技術との連携が進み、リアルタイムでの加工状況の監視や自動補正が一般化することで、さらに高精度・高効率な研磨工程が実現するでしょう。たとえば、センサーから得られるデータを解析して研磨条件を自動的に最適化したり、部品ごとの微妙なばらつきを学習して研磨パターンを柔軟に変更するシステムが期待されます。
製造業においては生産性の向上と人手不足への対策が喫緊の課題となっており、多軸水平研磨技術の高度化はこれらの課題解決に大きく寄与すると考えられています。今後の研究開発では、より小型化・軽量化された装置や、エネルギー使用量を最適化した持続可能なシステムが求められる見込みです。また、再生可能エネルギーの活用と組み合わせることで、環境負荷をさらに低減した研磨プロセスの確立も視野に入っています。
一方で、複雑な形状を持つ部品やアディティブ・マニュファクチャリング(3Dプリント)によって生み出される多様な素材への対応がこれからの大きなテーマとなります。多軸水平研磨技術がこれらの先端分野と相互補完的に発展すれば、従来では実現し得なかったほどの精密性とデザイン性を両立させた製品開発が加速することでしょう。
さらに、国際的な競争力を高めるためにも、標準化や規格制定への取り組みが進められています。多軸水平研磨技術の特性や安全基準、品質評価の方法を産業界全体で共有することで、有用な市場競争と技術革新が促進されると期待されています。こうした流れの中で、多軸水平研磨技術は製造工程の一部にとどまらず、今後の産業を支える基盤技術として位置づけられていくのではないでしょうか。
まとめ
多軸水平研磨技術は、製造業にもたらす革新性と高い応用可能性によって注目を集めています。従来の研磨手法では実現しにくかった複雑形状や多様な素材への対応が可能となり、品質面やコスト面、そして環境面でも多くのメリットを生み出します。自動車や航空宇宙、医療機器、さらには電子部品製造まで、幅広い分野での活用事例が増えており、その効果は既に大きな成果を上げています。
多軸制御による効率的な研磨プロセスは、今後さらに進化する見通しです。AIやIoTとの連携で自動化やデータ活用が進むことで、品質安定性と生産性を同時に向上させることが期待されています。特に、多軸技術ならではの柔軟性と精密性は、今後の多品種少量生産や先端素材の加工ニーズにも十分対応可能であり、製造工程の新たな標準となる潜在力を持っています。
スエナミ工業では、多軸水平研磨技術に対応した研磨装置や高品質の砥石、ブラシなど、多彩な製品ラインナップを取りそろえています。独自のノウハウを生かした制御システムも提供しており、初めて導入される企業でも安心して高精度の表面仕上げを実現していただけるでしょう。複雑形状や特殊合金などの加工にも適した製品を多数揃えているため、幅広い業種・用途でご活用いただけます。
今後もさらなる研究開発と標準化の取り組みにより、多軸水平研磨技術はより広範な産業領域に普及していくことが見込まれます。新素材や新プロセスとの組み合わせが、新たな製造メソッドを生み出す原動力となるでしょう。