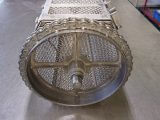
ワイヤーカット放電加工の基礎知識と最新技術動向
目次
はじめに
ワイヤーカット放電加工とは、細いワイヤーに電流を流し、その放電エネルギーによって金属などの電気伝導体を溶融・除去しながら切断する加工方法です。一般的には真鍮やモリブデンといった導電性の高いワイヤーが用いられ、微細な形状の加工にも対応できるため、金型や精密部品の製造に広く活用されています。電極ワイヤーと加工対象との間で高周波パルスが生じることで局所的に高温が発生し、材料を効率よく削り取る点が大きな特徴です。
この技術は、切削工具を用いずに金属を切り出せることから、複雑な形状や硬度の高い素材にも柔軟に対応できるという利点を持ちます。初期費用や維持コストが高めである一方、他の加工方法では難しい高精度な結果が得られることや、一度に多数の部品を同時に加工できる可能性もあるため、多くの製造業で重宝されています。さらに、近年は自動化技術やAIが導入されることで、生産性の向上や品質管理の効率化も進んでいます。本記事では、そうした技術革新の動きや将来の展望にも触れ、幅広い視点でワイヤーカット放電加工の魅力を解説します。
ワイヤーカット放電加工の仕組み
基本原理
ワイヤーカット放電加工の基本原理は、通電可能なワイヤー電極と加工物の間にごく短時間の放電を繰り返し発生させ、その熱エネルギーによって材料を融解または蒸発させて除去することにあります。高周波パルスを制御することで、余分な溶融部の拡大を抑えつつ、精密な形状を削り出せる仕組みです。
使用する機械と装置
この加工を行うには、ワイヤー電極の供給装置と巻取り装置、工作物を固定する治具、そして放電用の電源装置を備えた専用のワイヤーカット放電加工機が必要となります。一般には加工液として絶縁性の液体や純水を使用し、精巧な放電制御を可能にします。
加工プロセスの流れ
まず、専用の加工プログラムを作成し、ワイヤーを工作物に近づけて放電を開始します。ワイヤーは一定速度で送り出され、工作物との間に隙間を保ちつつ溶融を繰り返すことで材料を少しずつ除去します。切断が完了すると、ワイヤーは廃棄またはリサイクルされ、加工物は目的の形状に仕上がります。これらの工程は加工条件や材料特性に応じて細かなパラメータを設定する必要があり、高度な制御技術が要求されます。
ワイヤーカット放電加工の利点と欠点
利点
高精度加工
ワイヤーカット放電加工は、数ミクロン単位の誤差で切り出すことも可能であり、他の機械加工法では難しい高い精度を実現します。工具摩耗の影響が少なく、連続して均一な品質を保ちやすい点も大きな強みです。
複雑形状の加工
ワイヤーが通る隙間さえ確保できれば、極めて入り組んだ形状や微細な加工にも対応できます。金型の製造や機械部品の試作など、設計の自由度を高める要素として多くの現場で重宝されています。
使用材料の多様性
放電加工は、電気を通す素材であれば基本的に加工可能です。そのため、高硬度の金属や難削材、特殊合金などさまざまな材料に応用でき、広範な産業分野で利用されています。
欠点
加工速度の制約
放電エネルギーで徐々に材料を除去するため、切削加工と比較して加工速度が遅い傾向にあります。大量生産を短時間で行いたい場合には不向きな面もあり、生産ラインに導入する際には留意が必要です。
高コスト
専用の放電加工機やワイヤー電極、加工液などの設備投資が大きく、メンテナンスにも手間や費用がかかります。一方で、高精度加工を要する分野ではそのコストに見合う価値があるともいえます。
ワイヤーカット放電加工の用途
航空宇宙産業
エンジン部品やタービンブレードなど、高度な耐熱性や精度を要する部品の製造に利用されています。高硬度合金や難削材の加工が多いため、放電加工の特長を最大限に活かせる領域として注目度が高いです。
自動車産業
エンジン部品やトランスミッション部品など、複雑な形状が求められる部分に対しても効率的に対応できます。金型製作や試作段階でも活用され、新たなデザインや素材を用いた開発を支えています。
医療機器
医療分野では精密加工が必要なインプラントや手術器具などにワイヤーカット放電加工が導入されています。医療材料は特殊合金やチタン合金などが多く、放電加工ならではの複雑形状の再現で、高品質な製品の提供が可能です。
電子部品
微小な電子部品や精密機器の金属部品の製造にも適しています。微細なパターンを高精度で成形できるため、電子基板やメカトロニクス分野においても重要な位置を占めています。
最新技術動向
自動化とAIの導入
昨今は生産性向上を目的に、CAD/CAMソフトウェアとの連携やロボットによるワーク交換システムなど、自動化技術が積極的に導入されています。加えて、AIを活用した加工条件の最適化や不良検知も研究が盛んで、熟練技術者のノウハウをデータ化し、作業効率と品質を高める取り組みが加速しています。
微細加工技術の進化
ワイヤー径のさらなる微細化や制御精度の向上により、より小さな部品の加工が可能になっています。マイクロメートルレベルの寸法公差が求められる半導体関連や光学部品の製造でも、ワイヤーカット放電加工がその存在感を示しつつあります。
環境に優しい加工技術
加工液やワイヤー材のリサイクル率を上げる取り組みや、省エネルギー設計の機械開発など、環境負荷を低減する技術革新も続いています。産業界ではサステナビリティが重視されるため、こうしたエコフレンドリーな方向性は今後も重要となるでしょう。
ワイヤーカット放電加工の未来展望
技術の進化による新たな可能性
さらなる高速化や超精密化が期待され、機械学習やビッグデータ解析を組み合わせた最適制御技術も研究されています。これにより、従来は実現が難しかった超微細な加工や特殊環境下での応用など、今まで以上に幅広い産業分野での活用が見込まれています。
持続可能な製造プロセスの実現
環境保全と経済性の両立が課題となる中、廃液処理や資源の再利用を視野に入れた加工システムの研究が進みつつあります。同時に、エネルギー効率を高める技術開発や、ワイヤーおよび加工液のリサイクル技術向上が重要視され、将来的にはゼロエミッションをめざす取り組みも進展していくでしょう。
まとめ
ワイヤーカット放電加工の現状と将来性
ワイヤーカット放電加工は、複雑形状の製造や高硬度素材の精密加工に特化した技術として、製造業において欠かせない存在となっています。高品質な部品を安定して生産できる反面、コスト面や速度面での課題が指摘されています。しかし、AIやIoTを活用した高度な制御技術の発展により、課題を克服しつつ新たな可能性を見いだす段階に入っています。特に、自動化やデジタルツールとの連携が進む今日では、大量生産と高品質を両立させる手段としての価値も高まり、部品のトレーサビリティや多工程とのシームレスな結合も期待されています。ワイヤーカット放電加工がこうしたニーズに対応するためには、ソフトウェアおよびハードウェアの包括的なアップデートが欠かせません。
産業界における重要性と影響
自動車、航空宇宙、医療機器など、精度と信頼性が求められる製造現場では、ワイヤーカット放電加工の適用範囲がますます拡大しています。異なる素材や形状に対する柔軟性と安定した品質管理は、イノベーションを推進する重要な要素です。今後の技術開発によってさらなる効率化と高付加価値化が進めば、生産現場だけでなく社会全体に与える影響も大きくなるでしょう。
今回のコラムに関連して、スエナミ工業では多様な材質と複雑形状に対応可能なワイヤーカット放電加工のための最適な製品を提供しています。高精度な加工ニーズに応えながら、コストパフォーマンスや環境負荷削減にも寄与する優れた選択肢です。機器導入の際には、ぜひスエナミ工業製品をご検討ください。また、専門知識を取り入れたアフターサポート体制も充実しており、初めてワイヤーカット放電加工を導入する企業でもスムーズに稼働できるようサポートします。技術相談から試作品の制作に至るまで、幅広いニーズに対応可能です。