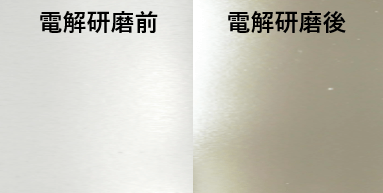
電解研磨による不銹鋼表面処理の効果と応用例
目次
1. はじめに
電解研磨とは
電解研磨は、不銹鋼やアルミニウムなどの金属を「陽極」として電解液に浸し、陰極との間に電流を流すことで金属表面を溶解させ、平滑化・光沢化を実現する表面処理技術です。従来の機械研磨や化学研磨とは異なり、金属表面を微細に除去する過程を電気化学的に制御できるため、複雑な形状や微細なパーツでも均一な仕上がりを得やすい点が特筆されます。近年では医療機器や食品産業、半導体製造装置など高度な衛生管理や高精度が求められる分野を中心に、その優れた処理能力が注目されています。また、電解研磨は表面にクロムリッチな酸化皮膜(受動皮膜)を形成させることで、耐食性を大幅に向上させる効果があることも大きな特徴です。
金属表面を美しく仕上げる手段としてはバフ研磨や研磨材によるブラスト処理なども存在しますが、電解研磨は研磨材との直接接触が少ないために素材の損傷を最小限に抑えられる点や、複雑な形状であっても均一に処理できるという利点が挙げられます。一方で、電力コストや専門的な設備が必要なことなどから、必ずしも全ての金属加工に向いているわけではありません。しかし、要求される仕上がりの精密度や高水準の清浄度などを考慮すると、電解研磨の果たす役割は今後さらに拡大していくと考えられています。
不銹鋼表面処理の重要性
不銹鋼は腐食に強く、耐久性や衛生面に優れていることから、食品加工機械や医療機器、建築資材など多種多様な用途に活用されています。ステンレス特有の酸化皮膜は大気中で自然に形成されますが、部品の製造過程や使用環境によっては、その皮膜が部分的に破壊されたり、不均一になったりすることがあります。このような場合、腐食が局所的に進行し、見た目や性能に悪影響を及ぼす懸念が生じます。
そのため、不銹鋼の表面をより安定化し、均一な酸化皮膜を形成して高い耐食性を保持することは極めて重要です。電解研磨を利用すれば、研磨と同時に酸化皮膜を再構築する過程が進み、不銹鋼本来の特性を最大限に引き出せるようになります。加えて、表面の凹凸や微細なバリを除去することで洗浄が容易になり、微生物や異物の付着を抑える効果も期待できます。特に医療現場や食品加工プロセスでは衛生面や安全性が厳しく求められるため、電解研磨による不銹鋼表面処理が重要な役割を担っています。
不銹鋼の美観や機能を確保・維持するために、適切な表面処理は必要不可欠です。電解研磨は単に見た目を美しくするだけでなく、機能面での向上も同時に狙える総合的な手法として、広範囲の産業分野で活用されているのです。
2. 電解研磨の原理
基本的なプロセス
電解研磨は、まず被加工物である金属を電解液の中に浸し、そこに陽極として電圧を加えることで実施されます。陰極には導電性を備えた素材(一般にはステンレスや炭素棒など)が使用され、電解液としてはリン酸や硫酸など、不銹鋼の表面を溶解しやすい組成のものが用いられます。陽極から溶け出した金属イオンは電解液中に拡散し、一部は陰極側に引き寄せられながら電気的に中和されるか、あるいは被加工面が均一化するように取り除かれます。このような原理により、微妙な表面の凸部が集中的に溶解されて凹部との差が減少し、最終的には平滑で光沢のある表面が形成されるわけです。
プロセスを進めるうえで重要な要素として、電流密度と電解液の温度管理があります。電流密度が高ければ速やかな金属溶解が進みますが、表面に不均一が生まれたり焼けを引き起こすリスクが高まる場合もあります。逆に電流密度が低い場合は研磨速度が遅く、生産性を確保するのが難しくなります。一方、電解液の温度管理も同様に重要で、適切な温度範囲を超えると電解液が過度に反応し、仕上がりが粗くなる恐れがあります。最適な条件を見極めるためには、素材の特性や求められる表面品質に応じたパラメータ調整が欠かせません。
電解研磨の化学反応
電解研磨時に発生する主な化学反応は、陽極側における金属の酸化と溶解です。例えば不銹鋼の場合、Fe(鉄)、Cr(クロム)、Ni(ニッケル)といった合金元素のイオン化が進み、Fe2+やFe3+、Cr3+、Ni2+などの形で電解液中に溶出します。また、電解液中での酸化還元反応によって生じる酸素が、表面を酸化しながら微細な凸部を優先的に溶解させることも特徴的です。
特筆すべきは、電解研磨によって不銹鋼表面に形成される酸化皮膜が、クロムを豊富に含んだ受動皮膜になりやすい点にあります。通常、不銹鋼の耐食性は表面に形成されるクロム酸化物によって保たれますが、電解研磨後はクロム濃度の高い層が表面を覆うため、耐食性能がさらに向上するのです。これにより、使用環境が過酷な場所でも長期的に不銹鋼の特性を維持しやすくなります。ただし、適切な電解液組成や工程管理を行わない場合には、表面にムラが生じたり、溶解しすぎて素材強度が低下するといった問題も生じ得るため、綿密なプロセス制御が必須となります。
3. 電解研磨の効果
表面の平滑化
電解研磨の最大の特徴の一つは、表面を平滑に整える能力です。加工物表面を刺激する研磨材を使用する機械研磨では、微細な傷や粗さがどうしても残りやすいですが、電解研磨では微視的なスケールで凸部が先に溶解されるため、より均一な仕上がりが可能となります。特に複雑な形状や微小領域が多い部品に対しては、従来の研磨方式では到達しにくかった部分の平滑化を効率的に進められるため、医療用カテーテルや電子部品などの微細加工分野で重宝されています。また、平滑化された表面は汚れや細菌の付着が少なく、清掃がしやすくなるメリットもあります。
耐食性の向上
不銹鋼表面で重要となるのが耐食性です。一般的に、不銹鋼は表面に自然発生する不動態皮膜によって酸化や腐食が進行しにくくなっています。しかし、使用条件や加工方法によっては皮膜が不安定になることもあり、局部腐食のリスクが高まる場合があります。電解研磨を実施すると、表面を均一に溶解して細かな傷や不純物を取り除くと同時に、クロムリッチな酸化被膜が再構成されます。これによって耐食性がさらに向上し、水や化学薬品に長時間さらされる環境でも腐食の進行を抑制しやすくなります。実際、医療機器や食品設備など高い清浄度と耐久性が要求される場面では、電解研磨した不銹鋼部品の寿命は大きく引き延ばされています。
見た目の美しさ
電解研磨により得られる表面光沢感は、機械研磨だけでは得にくいレベルまで達することがあります。鏡面仕上げに近い状態まで整えられた不銹鋼製品は、外観品質が重視される建築用内装材や装飾品などでも映えるため、デザイン性の高い製品に採用されるケースが増えています。従来のバフ研磨や研磨材を利用する機械的な手法に比べて、表面に研磨痕が残りにくい点もメリットです。視覚的な美しさはもちろんですが、平滑な面は指紋や汚れも除去しやすいという機能的な利点にもつながります。
生物適合性の改善
医療分野における不銹鋼部品は、カテーテルやステントなどの体内挿入部品から手術器具、人工関節部品など多岐にわたります。これらの部品には生体組織との接触面が多かったり、血液と接触する可能性が高かったりするため、高レベルの生物適合性が求められます。電解研磨で表面を平滑化し、目に見えない微小領域の凹部や汚染物質を取り除くことで、組織との摩擦を減らし、細菌などの微生物付着を抑制できるとされています。また、電解研磨後の不銹鋼表面はクロム濃度が高まり、腐食生成物が少なくなるため、体内へのイオン溶出リスクを低減できる利点もあり、医療機器の品質向上に大きく貢献しているのです。
4. 電解研磨の応用例
医療機器における利用
医療機器は人体へ直接的または間接的に影響を及ぼすため、衛生面、安全性、耐久性に関する厳格な基準が項目として定められています。特にステンレス製の外科用はさみやメス、歯科用器具、内視鏡用部品など、患者の体内・体外を問わず使用される器具は腐食への強さだけでなく、表面に付着した微生物を簡単に除去できる平滑さが必須です。電解研磨で処理された医療器具は、殺菌消毒工程における汚れ除去がしやすいため、再利用時の感染リスクを大幅に低減できます。優れた仕上がりと耐食性が相まって、機器の寿命を長く保つことにも寄与し、医療現場のコスト削減や患者の安全に貢献しているのです。
食品産業での活用
食品産業においても、機器や容器の表面が清潔であることは非常に大切です。食品残渣や微生物が付着しにくく、かつ洗浄しやすい設備を構築するためには、表面処理技術が欠かせません。電解研磨を施した不銹鋼タンクやパイプは、表面が滑らかで異物の溜まりを最小限にできるほか、洗浄時の水や洗剤などが表面全体に行き渡りやすい点がメリットです。また、長期的な使用環境(高温多湿、酸・アルカリなどの化学薬品使用)でも優れた耐食性を発揮するため、製品の品質維持と衛生管理の両面で食品産業に貢献しています。ビールの醸造タンクや調理器具、牛乳の配管などをはじめとする数多くの分野で、電解研磨が用いられるケースが増え続けています。
半導体製造プロセスへの適用
半導体業界では、クリーンルーム環境で製造装置や搬送装置が運用されるため、微小な異物の混入が製品不良につながりやすいという特徴があります。そのため、装置の構成部品には極めて高い清浄度が求められます。不銹鋼部品を電解研磨することで、微粒子の付着を低減し、洗浄プロセスでの除去率を高めることが可能です。とりわけエッチング液や薬液を扱うタンク、配管、バルブなどには耐食性が求められるため、電解研磨を施して表面の平滑化と耐久性向上を同時に実現し、半導体製造ラインの安定稼働に寄与しています。また、電解研磨後の表面状態が精密に評価されることで、より高度な品質管理を行える点も利点の一つです。
建築や装飾分野での利用
不銹鋼は建築外装や内装、エクステリア、家具の装飾など、多彩なデザインに用いられています。その際、表面の美しさや独自の質感が重視され、手入れのしやすさや耐久性も評価基準となります。電解研磨による鏡面仕上げや滑らかな表面仕上げは、モダンで高級感のある意匠を演出しつつ、傷や汚れが付きにくく、メンテナンスを容易にする効果を持ち合わせています。公園や商業施設でのオブジェ、看板、手すりなど、人目につく部分に利用されると見栄えの点でも魅力的で、かつ長期的な美観維持が期待されるのです。
5. 電解研磨のメリットとデメリット
メリット: 高精度・均一性
電解研磨最大の利点は、材料を選択的に溶解することで得られる高水準の平滑度と均一性です。研磨材を接触させて削る機械研磨では、どうしても研磨痕や磨きムラが生まれやすいですが、電解研磨は化学的な溶解を中心としたプロセスであるため、複雑形状や細かなエッジ部分まで均一に処理が行えます。また、再現性が比較的高く、同じ条件下で多くの部品を加工しても、均質な仕上がりが期待できる点が大きなメリットです。
さらに、電解研磨工程と同時に不純物や微小なバリ、酸化物膜が除去され、クロムリッチな層が再構築されることから、機能面での向上と見た目の向上を一括して狙えます。これらの特性は、厳しい品質管理基準を設ける産業分野では非常に魅力的であり、医療や半導体など、エラーが許されない場面で重宝されています。
デメリット: コスト・電力消費
一方で電解研磨にはコスト面と環境面の課題があります。まず、専用の電解液や電源装置、温度管理システムなどを導入しなければならず、初期投資が高額になりやすいことが挙げられます。また、安定した電源が必要とされ、加工の度合いによっては大きな電力を消費するため、電気代が膨らむ可能性もあります。さらに、電解液を定期的に廃棄または再生成するプロセスが必要となるケースが多く、環境負荷を抑えるための廃液処理費用や安全対策費用がかかる点も無視できません。
また、大型の部品には大きな槽や強力な電源が必要となるため、装置の規模が大きくなりがちです。これにより工場内のスペースを圧迫したり、設備の運用コストが増加したりといった面がデメリットとして考えられます。小型部品や高付加価値の部品には有効な場合が多い一方、低コストを最重視する大ロット生産では別の表面処理法を選択することも珍しくはありません。技術的なメリットが大きいだけに、コストや環境への配慮が十分に行われる必要がある技術だといえます。
6. 電解研磨の安全性と環境影響
安全な作業環境の確保
電解研磨は、強酸性もしくは強アルカリ性の電解液を使用するため、作業者の安全管理が非常に重要となります。防護具の着用や換気装置の整備、薬品の取り扱いに関する明確なマニュアル作成など、企業として充分な対策を講じることが不可欠です。また、電解研磨時にはガスが発生する可能性もあり、適切な換気を行わないと作業環境が危険にさらされる恐れがあるため、室内の酸素濃度や有害ガス濃度を常時モニタリングするシステムを導入するケースも増えています。
さらに、電気的な危険性も考慮する必要があります。高電流を使用する工程では、設備の絶縁対策や漏電ブレーカーなどの安全装置の導入が重要です。万が一のトラブルに備えて、作業マニュアルの徹底や緊急時の対応訓練を行っておくことで、事故発生リスクを最小限に抑えられます。
環境への配慮と廃液処理
電解研磨で利用される電解液はリン酸や硫酸などの強酸が主体となることが多く、使用後の廃液には金属イオンや反応生成物が含まれます。これらを適切に処理しないまま排出すると、環境汚染を引き起こす可能性があるため、廃液の中和や回収が義務付けられています。産業廃棄物や野放しの化学物質処理に対する規制は年々厳しくなっており、企業にはコンプライアンスを守るための設備投資と運用コストが求められます。
近年では、電解液を可能な限り再利用する技術や、廃液から金属イオンを回収してリサイクルする取り組みも進んでいます。コスト削減と環境負荷の低減を両立させるため、電解研磨を採用する企業ではプロセス自体の効率向上だけでなく、循環型社会の一端を担う技術開発にも力を注いでいます。これらの取り組みによって、社会の求める環境責任を果たしつつ、持続的な生産活動を続けることが可能となるのです。
7. まとめ
電解研磨の重要性と今後の展望
電解研磨は金属、特に不銹鋼に対して平滑化や耐食性向上、衛生面での利点を与える高度な加工技術として、多岐にわたる分野で利用されています。医療、食品、半導体、建築・装飾など数多くの用途があり、それぞれの分野で独自に電解研磨の恩恵を受けています。従来の機械研磨や化学研磨では困難だった複雑形状や高精度が必要な箇所にも対応でき、かつ表面をクロムリッチな酸化皮膜で覆うという特性は、高い耐食性と美観、清浄度を実現するうえで極めて有益です。
一方で、電力コストや専用設備の導入費用、危険物を扱うリスク、廃液処理に関する規制対応など、実用化・普及にあたり克服すべき課題があるのも事実です。今後、加工条件を最適化してより効率化を図り、環境への負荷を軽減する技術が進んでいくことで、電解研磨の利用範囲はますます拡大が見込まれます。ナノメートルレベルの表面制御が要求される先進技術の発展や、持続可能な生産と環境保護の両立を目指す産業界において、電解研磨は必要不可欠な存在となるでしょう。
電解研磨の導入を検討する際には、製品の用途や求める表面品質、コスト構造、環境責任など多角的な視点から評価を行うことが重要です。正確な工程設計と安全管理が行われれば、電解研磨は高い付加価値をもたらす画期的な加工技術として、多くの事業領域で大きな成果をもたらしてくれるはずです。
今回のコラム記事に関連して、スエナミ工業では、ステンレス製品の電解研磨技術を最大限に生かした多種多様なパーツや部品加工に対応する製品ラインナップを取りそろえています。厳格な品質管理のもと、医療用器具・食品加工装置・半導体関連部品など、さまざまな分野のニーズに合わせた精密な電解研磨を実施し、ユーザーの皆様へ安定した高品質を提供しております。もし電解研磨を活用して製品クオリティをさらに高めたいとお考えでしたら、ぜひスエナミ工業の製品やサービスをご検討ください。