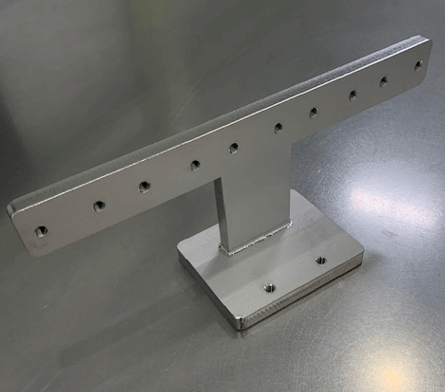
医療機器用ブラケットの製造方法と設計強度の最適化
1. はじめに
医療機器用ブラケットの重要性
現代の医療分野では、さまざまな機器が患者の安全と快適性のために使用されています。その中で、ブラケットは機器本体と付属パーツを安定的に連結するための重要な役割を担います。歯科分野はもちろん、外科用機器など幅広い分野で用いられ、高い精度と耐久性が求められます。
本コラムの目的と概要
本コラムでは、医療機器用ブラケットがどのように設計され、そしてどのような製造方法を経て高い強度と安全性を実現しているかを解説します。また、規制基準や材料選定、品質管理といった要素を総合的に捉え、未来へ向けた技術の可能性についても言及します。
医療機器用ブラケットのデザインや構造は、多様な機器の個別仕様に合わせて最適化される必要があります。患者の身体に直接かかわる場合には特に安全性を考慮し、滅菌や耐腐食性などの要件を満たすことが不可欠です。それに加え、メンテナンスのしやすさやコスト効率も重要となります。
こうした多面的な要求を満たすためには、各工程での精密な検証が欠かせません。設計段階では強度解析やモデル評価を行い、どのような荷重条件でも安全を維持できるよう配慮します。さらに、材料の特性や熱処理の有無など、微細な要素を組み合わせながら最適化を進めることが重要です。
こうして設計と製造の両面から丁寧に検討することで、医療機器に適合した高品質なブラケットが完成します。次章では、具体的な設計基準や材料選定の重要ポイントを詳しく見ていきます。
2. 医療機器用ブラケットの設計基準
設計の基本要素
医療機器用ブラケットを設計する際には、複雑な負荷条件を想定するだけでなく、長期使用における摩耗や経年変化にも対応できる設計が求められます。さらに、操作性や取り付けのしやすさといったユーザビリティの視点も重要となります。何度も交換しなくてもすむ設計を行うことで、医療従事者の負担軽減にもつながります。
材料の選定基準
使用材料は生体適合性や耐腐食性、強度特性などを考慮して選択されます。ステンレスやチタン合金などが一般的ですが、特定の医療環境では樹脂素材が選ばれるケースもあります。実際の用途や滅菌方法に合わせ、最適な素材を検討することが重要です。
金属材料の場合、腐食に強い被膜処理や表面研磨加工を施すことで、さらに耐久性を高められます。また、樹脂系は軽量性に優れる反面、衝撃に弱い場合があるため、使用環境に合った強度設計が必要です。
安全性と規制基準の考慮
医療機器は国内外の様々な規制をクリアする必要があります。特にブラケットは患者の身体に直接装着されるケースもあるため、生体安全性や滅菌性を証明できる厳格なテストを受けなければなりません。また、各国の承認制度に応じて書類や品質管理プロセスの整備が求められるなど、必要な要件は多岐にわたります。
そのため、設計段階から使用環境に即した認証要件を洗い出し、漏れがないようプロセスを構築することが、実用化への近道となります。特に海外市場を視野に入れる場合は、国際規格の理解と迅速な対応が必須です。
3. 製造方法の概要
伝統的な製造技術
従来は金属ブロックからの切削加工やプレス成形が主流で、一品ごとに丁寧に加工されていました。この方法は長い技術的蓄積があり、信頼性が高い反面、生産性に課題が残る場合もありました。微細な形状を再現するには職人の熟練が欠かせず、コストや納期にも影響が出ることが多かったのです。
一方、板金加工は比較的薄い金属板を曲げたり切断したりする技術で、軽量化を図りながらある程度の強度を確保できる利点があります。医療機器用ブラケットの場合、清潔性を保つための表面処理も重要であり、研磨やメッキなどの工程も丁寧に行われるのが特徴です。
これら伝統的な手法はいずれも熟練した作業者の技能が品質に大きく影響します。大量生産には限界があるものの、オーダーメイド品や小ロット生産では優れた対応力を発揮し、細部までこだわったカスタマイズが可能です。
最新の製造技術とその利点
近年では3Dプリンティング技術が急速に進化し、複雑な形状を持つブラケットでも高い再現性で製造できるようになりました。金属3Dプリントや樹脂3Dプリントは、従来工法では難しかった複雑な内部構造の実装を可能にします。
さらに、複合材料を用いた積層造形技術も注目を集めています。異なる材料を組み合わせることで、軽量化と強度を両立させ、耐久性を損なうことなく細かい調整がしやすいといった利点があります。
CADデータから直接製品を生産するプロセスは、設計変更の反映が容易であり、試作品の短期製造にも向いています。これにより、開発スピードが格段に向上し、市場のニーズにあわせた素早い対応が可能となっています。
4. 設計強度の最適化
強度解析の手法
医療機器においては、人為的な衝撃や繰り返し荷重など、さまざまな負荷が考えられます。そのため、有限要素法(FEM)などのシミュレーション技術を活用し、ブラケットのどの部分にストレスが集中するかを事前に把握することが重要です。
強度解析では、安全率を設定しつつ、製品が受ける応力やひずみを可視化します。特に破損リスクにつながる応力集中ポイントを洗い出し、形状や材料を最適化することで、実際の使用環境での安全性を担保します。
また、実験室での破壊試験や疲労試験など、物理的なテストと併用することで、シミュレーション結果の検証を行います。こうした多角的なアプローチにより、信頼性の高い設計を実現することができます。
設計の最適化プロセス
初期設計段階では、CADソフトを用いておおまかな寸法と形状を決め、強度解析によるフィードバックを繰り返し受けながらモデルを修正します。この反復的なプロセスが、最終製品のクオリティを大きく左右します。
最適化では、単純に厚みを増やすだけでなく、リブや補強材の配置、曲面などの幾何学的特徴を巧みに組み合わせることがポイントです。不要な素材を削減しつつ、必要な箇所には十分な強度を持たせるというバランスが重要となります。
さらに、コストや生産効率も並行して考慮されます。高価な素材を使用すれば強度は向上しますが、医療現場での使いやすさやメンテナンス性、そして患者負担との兼ね合いを踏まえて、総合的に最適な設計を目指します。
シミュレーション技術の活用
解析ソフトウェアを活用することで、温度変化や長期使用時の摩耗を仮想的に再現することも可能になります。実験だけでは短時間で把握しきれない経年劣化や部材の変形などをシミュレーション上で確認できるのは大きなメリットです。
特に、複合材料や新素材を用いる場合は、物性値が十分に把握されていないことも多く、シミュレーションと現実のギャップを埋めるためのデータ収集が欠かせません。継続的な実験と数値解析の連携こそが、信頼性の高い最終製品を生み出す鍵となります。
5. 製造における品質管理
品質管理の重要性
医療現場で使用される製品の不具合は、患者の安全を脅かすだけでなく、医療従事者にも大きなリスクを伴います。そのため、製造プロセス全体を通じて品質を管理し、問題の早期発見と対策を徹底することが必要不可欠です。
不良品削減のための対策
工程ごとのチェックポイントを設けることで、素材の欠陥や加工の誤差を早期に検出できます。例えば、寸法測定や外観検査だけでなく、強度テストや表面粗さの検証など、多角的な検査体制を整備することが効果的です。
さらに、不良品の原因分析にも力を入れる必要があります。不具合が起きた際に原因を追究し、設計、材料、加工条件など、問題を引き起こした要因を特定して再発防止策を講じることで、継続的に品質の底上げが可能となります。
継続的改善プロセス
品質管理は一度確立すれば終わりではなく、PDCAサイクルや継続的改善手法を用いて常にアップデートされるべきものです。新しい技術や材料が導入された際にも、既存の検査・管理手法を柔軟に変更して対応する姿勢が求められます。
また、現場の作業者や検査担当者とのコミュニケーションも不可欠です。作業手順や留意点を共有し、異常があれば誰もがすぐに報告できる仕組みを整えることで、不良品ゼロを目指す体制がより機能します。
6. 持続可能性と環境への配慮
エコフレンドリーな素材の使用
近年、環境への意識が高まるなか、医療機器用ブラケットの素材選定にもサステナビリティが求められています。リサイクル可能な金属や、再生プラスチックを利用することで廃棄物削減に貢献し、製造コストを抑えられる場合もあります。
製造プロセスの環境負荷低減
製造段階でも排水や排気ガス、エネルギー消費などの環境負荷を最小限に抑える努力が重要です。例えば、切削液を再利用できるクローズドシステムを導入したり、廃棄素材を再利用するリサイクル工程を整えるなど、各社がさまざまな工夫を重ねています。
また、CO2削減や省エネの観点から、生産ラインの自動化や効率化も検討されています。高度なロボット技術を導入することで、歩留まりを向上させつつ、エネルギー使用量を削減する取り組みが進んでいます。
7. 未来の展望
新技術の導入可能性
医療機器分野ではAIやIoTなどの先端技術が急速に進展しており、ブラケット設計にもこれらを活用する動きが見られます。センサーを組み込むことで、ブラケットの使用状況や負荷をリアルタイムで監視し、メンテナンス時期を予測するといった高度な管理も可能になるでしょう。
業界のトレンドと将来のチャレンジ
今後はますます個別化医療の時代へシフトしていく中で、患者ごとに最適な形状や材質を瞬時に提供できる生産体制が求められます。また、グローバルな規制の変化や複雑化に対応するために、デジタル化による一元管理システムの構築も課題となるでしょう。
さらに、新素材の研究開発や生体適合性を高める表面処理技術など、持続的なイノベーションが求められています。こうした取り組みを進めることで、より安全で信頼性の高い医療機器用ブラケットが世に出ていくことが期待されます。
8. まとめ
本コラムの要点の振り返り
本コラムでは、医療機器用ブラケットの設計と製造方法について、強度解析や規制基準、品質管理など多角的な視点から解説しました。患者の安全性を守るためには、素材選定から最終検査まで、一貫したプロセスの最適化が欠かせないことがお分かりいただけたかと思います。
医療機器用ブラケットの製造と設計強度最適化の重要性
今後も医療技術の進歩に伴い、ブラケットに求められる機能や性能は一層多様化していきます。そのため、設計強度の最適化や先端製造技術の導入は、医療機器の品質と競争力を高めるうえで極めて重要なファクターとなるでしょう。
スエナミ工業では、こうした医療分野のニーズに合わせた高品質の製品を取り揃えております。長年培ったノウハウと最新技術を融合し、ブラケットをはじめとする各種医療機器の設計・製造において、お客様の多様な要求に応えるソリューションをご提案いたします。
医療機器用ブラケットは、小さなパーツでありながら装置全体の機能を左右する重要な要素です。その設計や製造においては、厳格な品質基準と安全性の確保が必須であり、国際的な規制動向への適応も避けては通れません。今後の技術革新と相まって、さらなる高性能化と省コスト化が実現すれば、多くの医療従事者や患者にとって恩恵が大きいと考えられます。